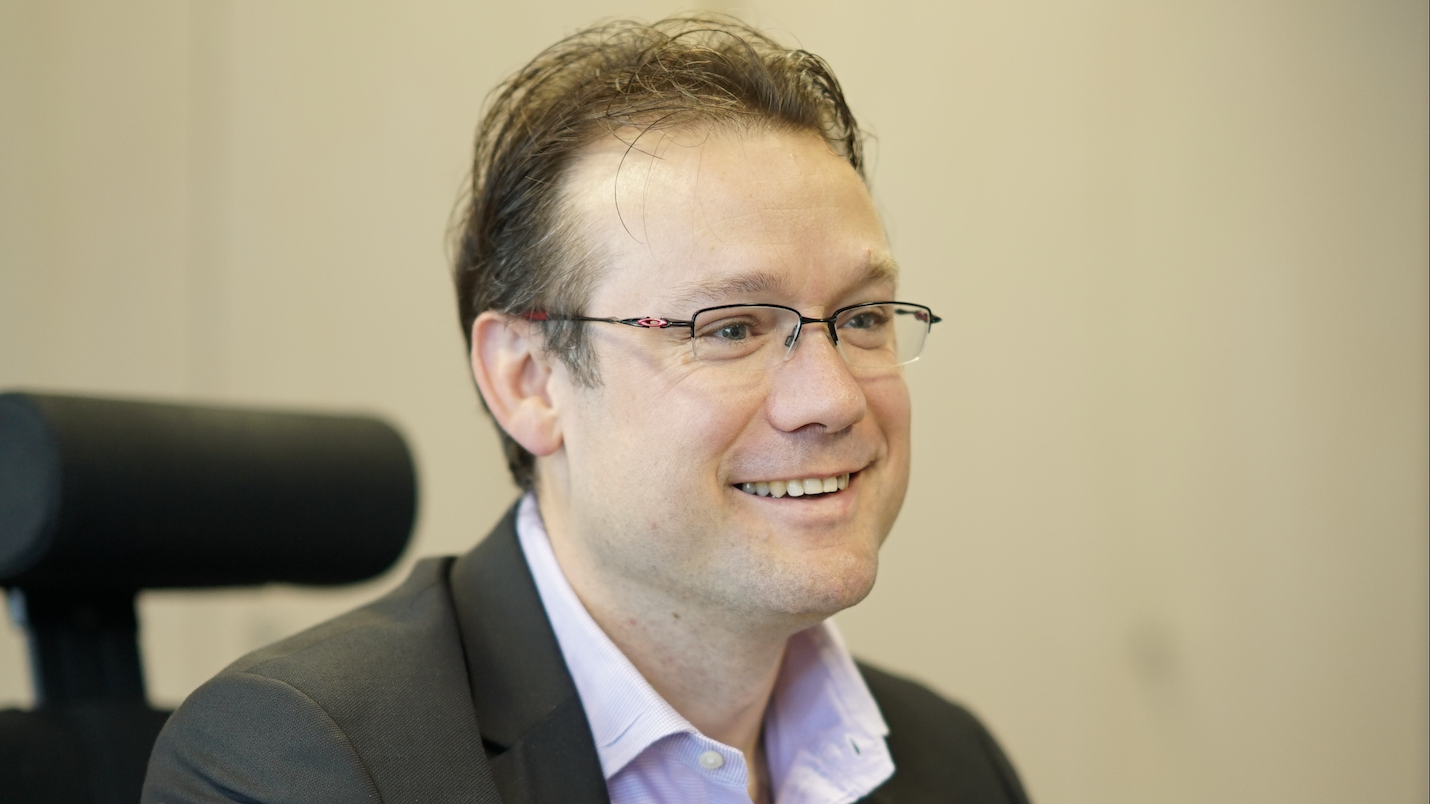
L’acier, matériau de choix pour relever le défi climatique
Réduire les émissions de CO2 liées aux bâtiments implique d’agir à tous les niveaux. La production de matériaux est évidemment impactante et l’acier, élément incontournable dans la construction mais aussi matériau le plus recyclé au monde, recèle encore un fort potentiel pour réduire son empreinte carbone.
Interview d’Olivier Vassart, CEO de STELIGENCE®, Groupe Arcelormittal
Pourriez-vous donner quelques chiffres significatifs du challenge que représente la décarbonation de la construction ?
Le secteur de la construction est responsable de 40 % des émissions globales de CO2. La moitié de l’acier produit au niveau mondial, tel que celui que nous fabriquons au Luxembourg, finit dans les bâtiments : structures, façades, toitures, mais aussi systèmes de ventilation et câblages. L’acier est donc directement concerné par cette problématique.
On estime, par ailleurs, que le nombre de m2 construits dans le monde devra être doublé d’ici 2050/2060 pour répondre à l’augmentation d’une part de la population et d’autre part de la surface construite par personne. Ce qui veut dire que, même si l’entièreté du bâti actuel était rénovée, il faudrait tout de même encore construire la même quantité de bâtiments que celle qui existe déjà.
Pour contribuer aux efforts de décarbonation, ArcelorMittal peut agir sur un levier qui est la réduction de l’impact environnemental de la production de l’acier. Comment vous y prenez-vous ?
Nous travaillons sur le cycle du carbone. Nous le faisons, par exemple, dans le projet Carbalyst®, mené sur notre site de Gand en Belgique, qui consiste à capturer le carbone sortant des hauts-fourneaux pour le réutiliser et générer de l’éthanol. Le CO2 transite par un système à base d’algues qui réagissent en produisant de l’éthanol, que nous distillons.
Nous essayons aussi de réduire notre impact CO2 à l’entrée des hauts-fourneaux. Nous avons investi dans une installation industrielle - toujours à Gand - qui s’appelle Torero. Elle a pour vocation de torréfier des résidus de bois et de plastique, qui sont ensuite injectés dans le haut-fourneau en remplacement d’une partie du coke.
Votre production au Luxembourg est composée à 100 % d’acier recyclé issu de chantiers de démolition, de vieilles voitures ou des parcs à containers. Qu’est-ce qui fait de l’acier le matériau le plus recyclé au monde ?
Premièrement, il est très facile à séparer des autres matériaux de par ses propriétés magnétiques. Ensuite, lorsqu’on refond de l’acier, on récupère de l’acier. C’est une boucle infinie.
L’impact environnemental de la production d’acier recyclé est-il beaucoup plus faible que celui d’une production primaire ? Combien de CO2 permet-elle d’épargner ?
Elle est effectivement plus faible, et ce d’autant plus que nous refondons les pièces, non pas avec du charbon, mais avec de l’électricité issue du réseau luxembourgeois où la part de nucléaire et d’énergie renouvelable est importante - donc les émissions de CO2 très faibles -, et nous avons aussi des accords avec des producteurs d’énergie renouvelable pour garantir un approvisionnement suffisant et pouvoir produire certains produits avec 100 % d’énergie renouvelable.
Il existe une autre technologie industrielle que je n’ai pas évoquée et que nous sommes les seuls à utiliser en Europe : la réduction directe. Ce procédé part du minerai de fer, mais l’acier en est extrait en utilisant du gaz, et non du charbon. Un haut-fourneau classique émet environ 2,4 t de CO2 / t d’acier produit. Lorsqu’un acier primaire est produit par réduction directe, ce chiffre est divisé par deux pour atteindre 1,2 t de CO2 / t d’acier produit. Nos usines luxembourgeoises de production d’acier recyclé ne dégagent que 500 à 600 kg de CO2 / t d’acier produit et si, en plus, on utilise de l’énergie renouvelable, on descend entre 300 et 350 kg de CO2 / t d’acier produit. Une poutrelle représente 333 kg de CO2 /t d’acier.
Et nous poursuivons nos efforts d’innovation en la matière. Nous sommes notamment en train de construire un nouveau four électrique à Belval, plus performant et moins énergivore que le four existant, qui représente un investissement de l’ordre de 67 millions d’euros.
Ces mesures sont-elles globalement suffisantes pour atteindre les objectifs de neutralité carbone ?
Non, bien sûr. Chaque maillon de la chaîne a un rôle à jouer : les fabricants comme nous qui ont la charge de diminuer l’impact environnemental des matériaux, mais aussi les architectes dont la responsabilité est de dessiner des bâtiments plus flexibles et les ingénieurs qui ont pour mission d’optimiser l’utilisation des matériaux, d’en utiliser le moins possible et de les mixer.
La plupart des bâtiments démolis aujourd’hui le sont, non pas pour des raisons structurelles mais parce que leur agencement intérieur ne correspond plus aux besoins des utilisateurs. Il est donc primordial de changer la manière dont on les conçoit : au lieu de créer des bâtiments avec des murs et des colonnes qui empêchent toute modularité, il faudrait y intégrer les évolutions futures et proposer de grands plateaux ouverts qui permettraient, par exemple, de passer d’un open space à des bureaux fermés ou des salles de réunion.
D’autre part, il importe de découpler les fonctions pour allonger la durée de vie des bâtiments. Dans de nombreux bâtiments, la façade est à la fois isolante mais aussi portante, ce qui signifie qu’on ne pourra pas la « déplugger » pour en installer une nouvelle quand la réglementation thermique aura évolué.
Un autre point essentiel est d’utiliser moins de matériaux et surtout de mieux les utiliser, c’est-à-dire de privilégier les matériaux à hautes performances et de les combiner intelligemment entre eux. Je suis un fervent défenseur de l’idée qu’il ne faut pas considérer qu’il existe un matériau supérieur aux autres, mais qu’il faut plutôt les associer de manière à exploiter les qualités de chacun. Dans cet esprit, je citerai un projet que nous avons avec l’Université du Luxembourg dans le cadre duquel nous travaillons sur la mixité acier-béton et acier-bois dans les bâtiments, des combinaisons qui permettent d’optimiser les structures et d’utiliser moins d’acier.
L’empreinte carbone d’un bâtiment tertiaire conçu avec des matériaux déjà disponibles comme le béton à haute résistance et l’acier à haute limite élastique, décarboné et produit au Luxembourg, est deux fois moindre que celle d’un bâtiment traditionnel.
Des coûts supplémentaires sont-ils à prévoir pour les bâtiments décarbonés ?
Ils se situent entre 1 et 2 euros/m2 construit seulement car la réduction de la quantité de matériaux induite par l’utilisation de matériaux plus performants compense l’extra demandé pour un matériau décarboné.
Une tendance émergente est la réutilisation des matériaux. L’acier s’y prête-t-il ?
Parfaitement, car les profils en acier sont standards. En Europe, ils sont assemblés sur site par boulonnage et sont donc démontables. De plus, un profil qui, dans un bâtiment, n’est pas soumis à la fatigue et est protégé de la corrosion a une durée de vie quasi-illimitée.
La Cour de justice de l’Union européenne au Kirchberg, par exemple, a été démontée et remontée par l’architecte Dominique Perrault il y a plusieurs années, tout comme l’ont été la bibliothèque de l’Université du Luxembourg, ce magnifique bâtiment en acier et en verre à Belval, et le bâtiment voisin.
Déconstruction et réutilisation sont des principes qui sous-tendent également le futur siège d’ArcelorMittal. Ce projet a vocation à montrer qu’il est possible de construire un bâtiment de grande hauteur avec une structure démontable et potentiellement réutilisable en acier décarboné, produit localement. Outre la démontrabilité, ce bâtiment incarne tous les aspects que je vous ai décrits : une architecture sans poteaux sur une longueur de 18 m, une structure mixte et l’emploi d’éléments standards en acier à haute limite élastique.
Quels sont les freins au réemploi à grande échelle ?
Il faut que les bâtiments soient conçus pour être déconstruits. L’intention y est, mais les instruments incitatifs pour le faire ne sont pas encore en place : des subsides sont accordés à ceux qui réutilisent des matériaux, mais pas encore à ceux qui dessinent des bâtiments démontables.
Le problème n’est pas d’ordre technique, comme nous l’avons démontré dans le projet « Petite Maison » à Belval, mené de pair avec l’Université du Luxembourg et Béton Feidt. Cette maison a été conçue pour être entièrement démontable. Elle a d’ailleurs déjà été démontée et nous sommes en train d’étudier le vieillissement des matériaux pendant le stockage.
Puisque vous parlez de stockage, où entreposer les éléments démontés ?
Il est clair qu’une nouvelle économie est à mettre en place autour du stockage et de la réutilisation. Le marché de la construction est déjà organisé avec des stocks qui permettent d’approvisionner les différents chantiers. Il n’est pas exclu que ces stocks puissent également contenir une partie de matériaux réutilisés. Il existe déjà des stockistes aux Pays-Bas et en Angleterre qui gèrent un stock d’acier structurel récupéré, prêt à être réutilisé.
Mélanie Trélat