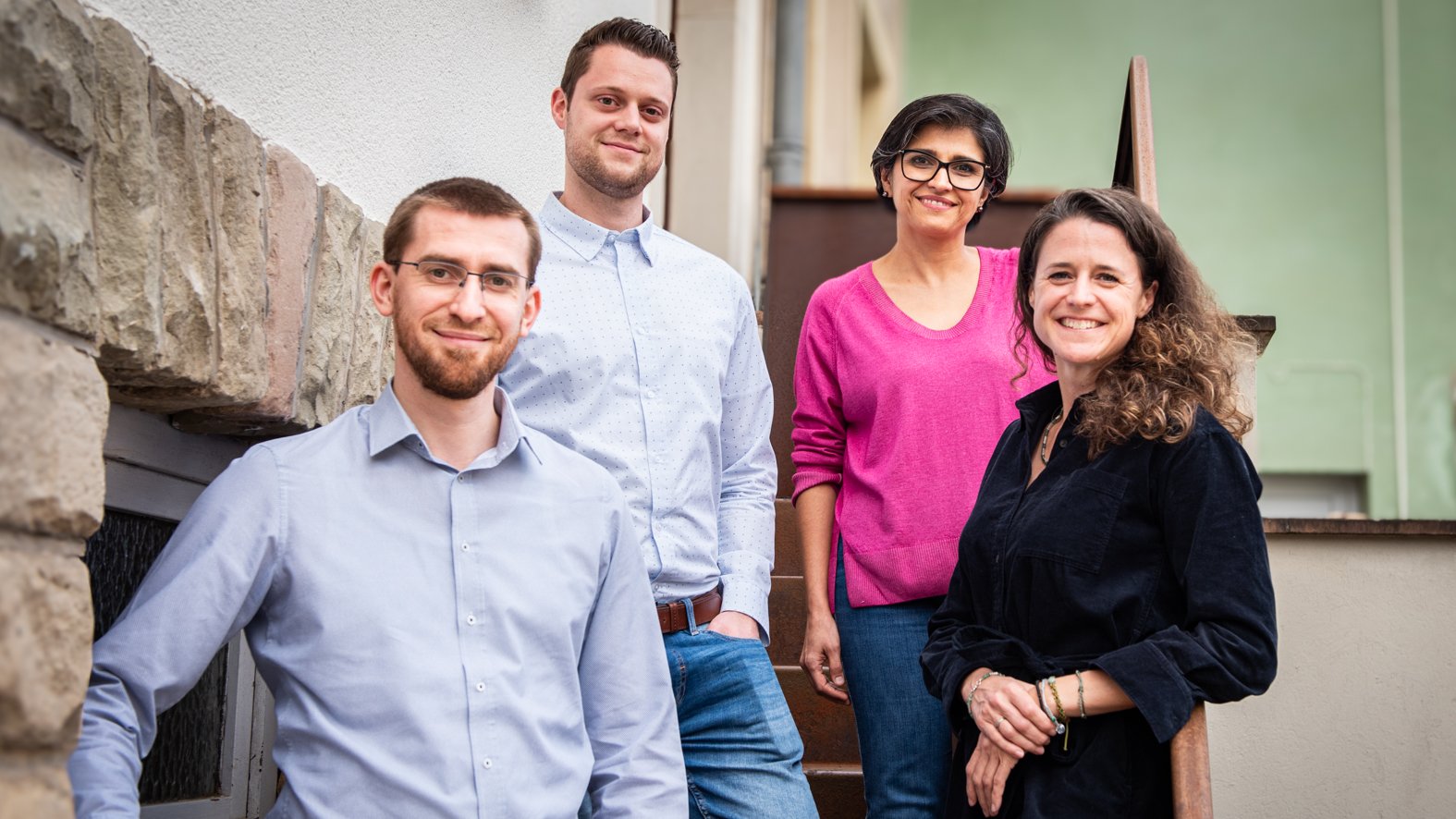
Minimiser l’impact : un travail d’équipe
C’est autour de la table que les solutions se façonnent. Une vision partagée par les quatre concepteurs des Glamping Cabins qui devraient voir le jour prochainement pour répondre au besoin d’hébergements touristiques du Luxembourg.
Rencontre avec Sahar Azari (Saharchitects), Lee Franck (LEEN), András Kozma (DESA) et Thomas Wenkin (Buildtec)
En mai 2023, Saharchitects remportait le concours d’architecture organisé par la Direction générale du tourisme et l’Ordre des architectes et des ingénieurs-conseils (OAI) avec son projet modulaire Glamping Tuurm / Tiermchen. Cet appel portait sur la création de logements touristiques en milieu rural. Sahar Azari, architecte : « Il nous a été demandé de développer des logements durables, inclusifs, faciles à installer et qui intègrent des éléments identitaires propres au Luxembourg ».
L’étape suivante consistait en la réalisation des plans d’exécution du projet, à fournir aux futurs investisseurs – qui semblent réceptifs, même si rien ne peut être annoncé à ce stade – et aux entreprises qui se chargeront de concrétiser la vision de Saharchitects. Pour cette mission, l’architecte a souhaité constituer une équipe multidisciplinaire. Rapidement, Lee Franck (LEEN, spécialiste décarbonation), András Kozma (DESA ingénieurs-conseils) et Thomas Wenkin (BuildTec, ingénieurs-conseils spécialistes des énergies renouvelables) ont rejoint Saharchitects dans la réflexion.
Pourquoi la réduction des émissions de carbone a-t-elle été une priorité pour ce projet ?
Lee Franck : Une stratégie circulaire était imposée par le cahier des charges, mais pas la décarbonation en tant que telle, qui n’est pas encore cadrée légalement au Luxembourg. Les deux sujets sont cependant liés et c’est pour cette raison que nous avons décidé de les traiter en parallèle. Nous voulions démontrer que nous disposons déjà aujourd’hui de leviers pour réduire significativement l’empreinte carbone des projets architecturaux. Et qu’il est inutile d’attendre que la demande vienne des clients ou de la législation.
Sahar Azari : Avec une experte en décarbonation au sein de l’équipe, à savoir Lee, nous disposions des connaissances utiles, et d’un petit projet tout à fait adapté à cette démarche.
Quelles solutions ont été retenues pour atteindre 37 % de réduction du carbone incorporé ?
András Kozma : Il y a deux dimensions à considérer quand on veut travailler sur l’empreinte carbone. La première, c’est le carbone produit par la construction aujourd’hui, qui peut être réduit grâce à un design efficace. Ensuite, il faut se pencher sur le carbone qui sera produit à l’avenir, et cela se fait en construisant un bâtiment durable, dans le sens où sa flexibilité permettra de l’adapter aux besoins futurs. De plus, nous avons appliqué les principes de conception pour la déconstruction et le réemploi (ou DfD – Design for Deconstruction), pour empêcher des déchets futurs. Pour cela, la standardisation et la modularité sont des aspects primordiaux. Nous avons gardé les mêmes types de sections d’acier et de bois partout, ce qui permet de les commander en plus grandes quantités et de réduire les émissions de CO2. C’est ensuite par modularité que nous obtenons des cabanes de plus petites (Explorer) ou plus grandes dimensions (Family).
Thomas Wenkin : Pour la partie technique, nous avons travaillé sur quatre axes, à commencer par la demande. En optimisant les besoins et donc en réduisant la demande, on fait baisser l’apport en eau et en énergie, tout en maintenant un confort optimum. Nous avons par exemple opté pour des équipements économiseurs d’eau – chasses et pommeaux à faible débit – et des appareils électriques peu énergivores, qui requièrent moins de panneaux photovoltaïques (PV) et de batteries de stockage pour fonctionner off-grid ; et donc moins de CO2 est émis par la production de ce matériel.
Ensuite, nous utilisons au maximum les ressources naturelles disponibles, comme le soleil avec le PV, l’air dans une ventilation naturelle, et l’eau de pluie qui est récupérée et circule par gravité, grâce à des réservoirs en hauteur.
Nous avons établi un tableau comparatif des avantages, inconvénients et prix des équipements techniques, auquel nous avons ajouté des données génériques concernant l’impact carbone lié à leur fabrication / utilisation. Cela a permis de nous tourner vers des solutions intelligentes, optimisées et bas carbone.
Enfin, la standardisation a aussi été appliquée aux équipements rassemblés dans la tour technique, et nous les modulons selon l’usage prévu.
SA : Tout cela est bien entendu possible, et même bienvenu, dans un logement touristique rural qui nous plonge en pleine nature. Par exemple, un poêle à bois est placé dans l’espace séjour et la chaleur traverse une grille dans la porte de salle de bains. Cela fait partie de l’expérience.
Nous avons aussi, dès le départ, décidé d’omettre les finitions et de maintenir les matériaux dans leur état brut. Cela facilite leur réutilisation parce qu’il n’y a ni colle, ni trou. Tout peut être réutilisé plus tard.
Comment travaille-t-on efficacement sur un tel projet commun ?
LF : Mon rôle au départ était de mettre le sujet de la décarbonation à plat, à l’aide d’un workshop pour partager ce savoir sur les stratégies qu’on peut mettre en place. Tout le monde venait aussi avec son expérience, et chacun a pu élaborer ses solutions pour la structure, l’architecture, la technique du bâtiment. Il était essentiel qu’on ait une équipe complète dès l’APS.
SA : Dès le début, nous nous sommes retrouvés toutes les deux semaines pour 3-4 h de brainstorming. Durant deux mois, on a peu dessiné, mais beaucoup échangé. Et puis dans le dernier mois, nous sommes vraiment passés en production. Je pense que la réflexion collective est nécessaire. Évidemment, cela a un impact sur le coût des honoraires, mais ça représente peu de choses par rapport au gain final sur la production.
TW : Dans ce type de collaboration, c’est important d’être tous sur la même longueur d’onde et d’avoir la volonté d’améliorer les choses. À mon sens, ça fonctionne bien en petit groupe.
AK : Comme chaque décision a des conséquences sur tout le reste, il est vraiment utile d’être tous autour de la table pour développer ensemble les solutions.
LF : Il faut rapidement identifier les hotspots carbone ; dans notre projet architectural assez minimaliste, c’était la structure. Ensuite il faut itérer, comparer et optimiser. Le plus important est qu’on ne travaille pas de manière cloisonnée. Au-delà de notre équipe réduite, nous avons eu la chance de pouvoir compter sur l’industrie pour guider nos choix de standardisation et méthodes de fabrication plus bas carbone, et sur l’Université du Luxembourg qui mène des recherches sur les connexions démontables dans les structures bois-acier. C’est une des premières fois que ces nouvelles méthodes vont être employées.
SA : Évidemment, le fait d’avoir un projet en structure légère a été un avantage considérable, car c’est bien moins réglementé. Cela nous a permis, par exemple, de travailler sur l’épaisseur du CLT. En passant de 18 à 24 mm, nous pouvons supprimer l’isolant et réduire la taille de la fondation. Nous obtenons une valeur U de 0,4 là où il faudrait 0,2 en construction classique. Nous avons aussi agi sur les fondations, en réduisant le béton au strict minimum et en utilisant du gravier en complément, qui a bien moins d’impact carbone.
J’aimerais beaucoup, à l’avenir, pouvoir intégrer une équipe élargie dès la conception, en impliquant également le constructeur et le client. Et qu’on puisse remettre en question les réglementations du secteur afin d’avancer dans la bonne direction !
Marie-Astrid Heyde