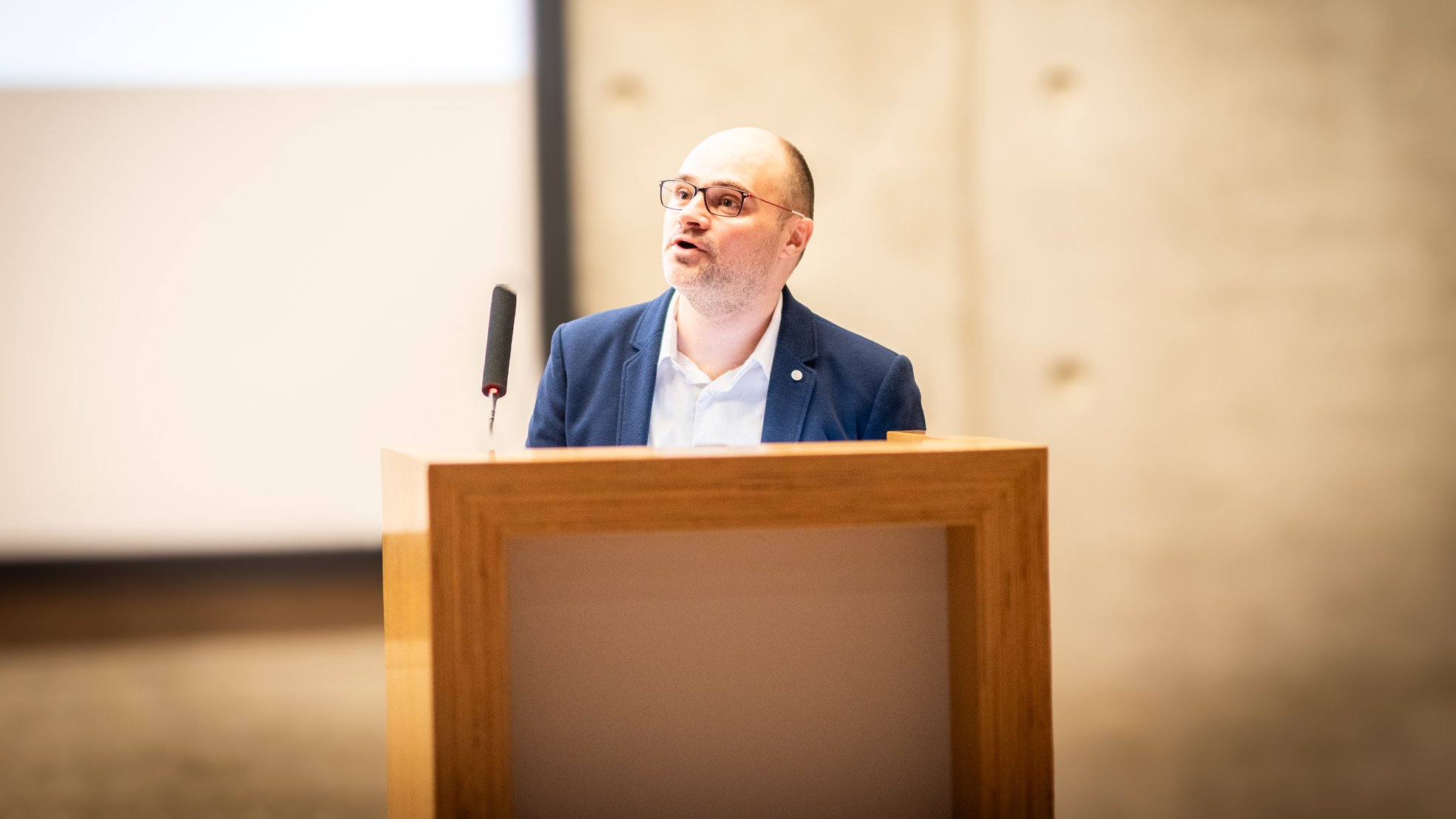
Pour une décarbonation transparente et saine de la menuiserie extérieure
Hydro a franchi un pas crucial en 2018, en mettant en place une approche holistique de réduction de son impact carbone basée sur trois piliers : produits, société et environnement. L’objectif est de diviser son bilan carbone par deux à l’horizon 2025. Fin 2023, il enregistrait déjà une réduction de 40 %. Tous les feux sont donc au vert.
Interview de Stéphane Hardy, Project Manager Luxembourg Hydro Building Systems
Comment votre démarche de réduction de votre impact carbone se traduit-elle dans les faits ?
Nous considérons la globalité de la vie du produit tout en gardant le focus sur ses performances thermiques et acoustiques. Avec le développement de produits à très hautes performances, l’incidence de l’impact de la partie construction d’un bâtiment est amenée à augmenter. Nous agissons donc sur l’ensemble de la chaîne : matériaux (aluminium, mais aussi polyamides), processus, transport...
La collaboration avec les architectes, ingénieurs, promoteurs, menuisiers et façadiers est essentielle. Nous travaillons, par exemple, sur l’intégration de nos systèmes dans des bâtiments d’habitation collective et de bureaux où une ventilation automatisée sera mise en place. Ce projet a donné lieu à de nombreuses réunions sur une approche industrielle qui impliquerait la préfabrication en usine d’éléments de murs dans lesquels les châssis seraient déjà intégrés.
En parallèle, nous réfléchissons à la démontrabilité. Il existe notamment un système de précadres où le châssis vient se raccorder directement qui a déjà fait ses preuves aux Pays Bas. Il permet une meilleure modularité, sans compromis sur la performance et en réduisant l’impact lié aux étanchéités et recouvrements de finition extérieure et intérieure.
Que mettez-vous en œuvre pour diminuer l’empreinte de vos produits ?
L’aluminium Hydro Circal 75R, qui contient au minimum 75 % d’aluminium post-consumé recyclé, est standard dans toutes nos séries des marques Sapa et Wicona. Il était à l’origine certifié par EPD à 2,3 kg de CO2 / kg d’aluminium, mais est passé à 1,9 kg de CO2 / kg d’aluminium, en début d’année. Il y a plusieurs raisons à cette baisse : notamment des investissements en faveur d’un approvisionnement énergétique plus vert, mais aussi le fait que la part d’aluminium post-consommé a augmenté pour s’élever à plus de 80 % aujourd’hui.
Nous continuons à innover. En 2023, nous avons réalisé les tout premiers projets en Hydro Circal 100R (100 % d’aluminium post-consumé recyclé), qui est certifié à 0,5 kg de CO2 / kg d’aluminium.
Hydro Circal 75R et 100R sont produits dans notre usine de Clervaux dont 120 000 t d’aluminium recyclé sont sorties l’année dernière.
Vous précisez que l’aluminium que vous recyclez est de l’aluminium post-consumé. En quoi cette nuance est-elle importante ?
L’aluminium post-consumé a déjà eu une vie, sous forme d’objet, alors que l’aluminium pré-consumé est issu de chutes d’extrusion. Autrement dit, ce dernier est un déchet dont l’utilisation n’est pas circulaire et n’apporte rien en termes d’impact carbone, puisque qu’elle force non pas le réemploi de l’ancien aluminium, mais la production de chutes, et nous ne voulons pas produire plus ! C’est un sujet qui fait débat au niveau des EPD, parce qu’il existe deux méthodes de calcul dont l’une donne une valeur zéro en termes d’impact carbone à l’aluminium pré-consumé. Or, ce n’est pas juste : il faut donner un poids carbone à l’aluminium pré-consumé !
Nous avons parlé d’aluminium, mais il y a aussi tous les autres composants : polyamide, joints, quincailleries, etc.
Nous travaillons avec nos fournisseurs pour décarboner le produit complet. Notre objectif est d’atteindre un ratio de 80 % de composants recyclés / 100 % recyclables sur nos nouvelles gammes d’ici 2025.
Notre dernière génération de murs-rideaux, par exemple, a été conçue sans silicone au niveau des jonctions, où il a été remplacé par des joints à découper et à comprimer. Les joints d’isolation thermique sont, eux, fabriqués à partir de bouteilles en plastique.
Nous nous associons également à des partenaires afin d’intégrer dans nos menuiseries des vitrages recyclés. L’impact carbone d’un élément de façade peut être réduit de plus de 50 % uniquement en passant par les bonnes chaînes d’approvisionnement en aluminium et vitrage.
Bien sûr, l’empreinte carbone de nos produits est chiffrée par EPD et nos logiciels sont prévus pour générer des EPD dynamiques, adaptées à chaque projet et, même, à chaque châssis.
Comment l’approvisionnement en aluminium post-consumé se passe-t-il ?
Les châssis et les façades aluminium sont nos mines, et elles se trouvent en Europe, ce qui permet de garder notre indépendance par rapport aux pays qui ont de la bauxite. Nous n’avons jamais eu, et nos extrapolations pour l’avenir ne montrent, aucun problème d’approvisionnement.
En revanche, il faudrait pousser la filière de rénovation et de récupération à son paroxysme car utiliser de l’aluminium recyclé, c’est bien, mais fermer la boucle de la récupération en permettant d’approvisionner Hydro CIRCAL dans les chantiers luxembourgeois de rénovation, c’est encore mieux. Sans cela, nous resterons dans un système d’économie linéaire, alors que l’objectif est de fermer la boucle et de passer ainsi de la durabilité à la circularité. Décarboner pour dire qu’on décarbone ne sert à rien. Il faut aller plus loin, vers une décarbonation plus saine. Et, encore une fois, les échanges, la transparence sont inévitables dans ce processus.
Un projet pilote au Luxembourg est en cours. Les anciens châssis que nous récupérons sont démantelés dans notre centre de Dormagen puis l’aluminium est envoyé dans notre centre de Clervaux où il est recyclé. Nous reviendrons plus en détail sur cette première dans un futur Neomag.
La digitalisation a-t-elle un rôle à jouer dans la décarbonation ?
Nous en sommes convaincus. C’est pourquoi nous attribuons un QR code à chaque produit, auquel sont liées toutes les données le concernant : dimensions, références des différentes pièces, performances thermiques et environnementales, processus de fabrication et de pose, valeur de fin de vie. Ce système permet ainsi au client de visualiser son châssis en 3D dans son mur via l’application Sapa. L’intérêt est même encore plus grand au niveau professionnel puisque l’objet peut être intégré dans une bibliothèque exploitable dans le BIM.
Mélanie Trélat